Digital twin platform for heat pumps
Acond streamlines anomaly detection with the Databricks Platform
Million new data rows daily
Heat pumps connected, uploading up to 60 distinct measurements every 5 seconds
Minutes of technician time saved per service callout
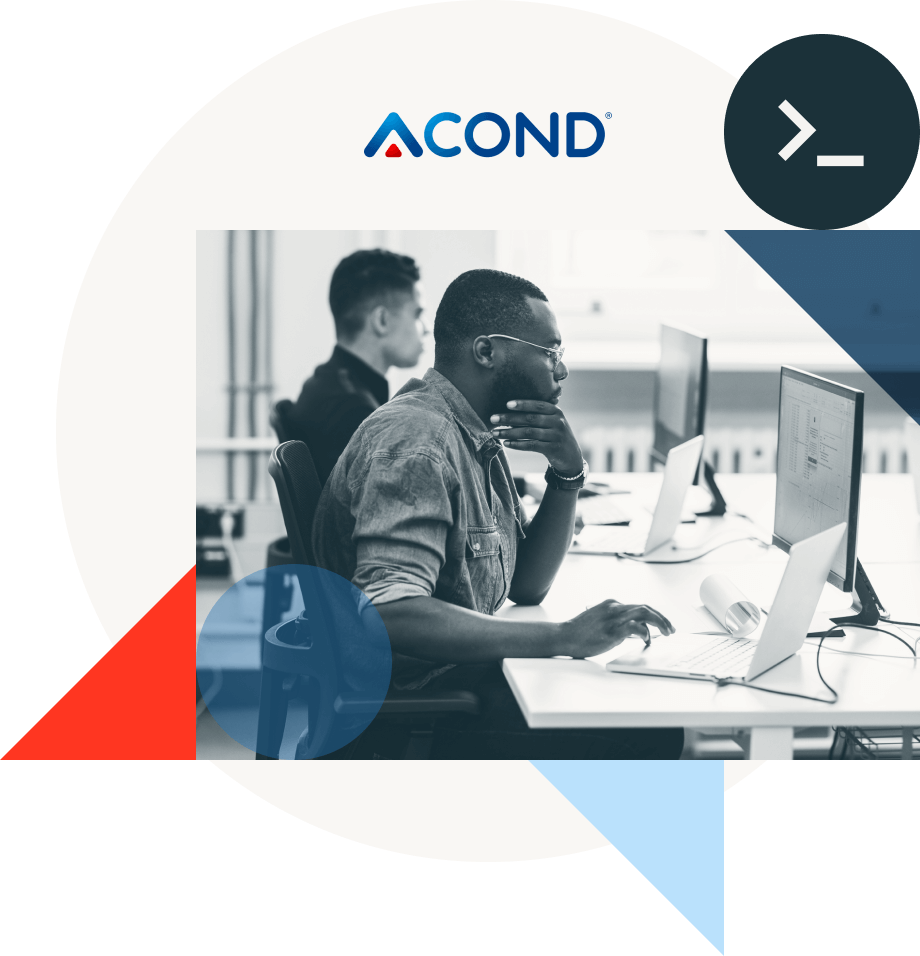
In an era where efficiency and sustainability are critical, Acond, a prominent European heat pump manufacturer, has adopted data-driven strategies to elevate their services. Faced with challenges in managing and analyzing data from their extensive network of installed heat pumps, the company turned to the Databricks Data Intelligence Platform. This transformation streamlined operations and significantly improved the reliability and efficiency of their heat pumps, demonstrating Acond’s commitment to pioneering future energy solutions.
Data analysis delays and limited insights hinder heat pump performance
Acond, a leading manufacturer of heat pumps, faced challenges in their journey toward digital transformation. The core limitation revolved around the slow and cumbersome data analysis processes from installed pumps, which lacked a comprehensive view and timely insights. Each pump, equipped with an SD card, gathered operational data crucial for understanding performance and diagnosing issues. However, whenever a pump encountered a problem, the data gathering and aggregation process by a technician took about 15 minutes per pump — a considerable time investment given the growing number of pumps serviced. This not only delayed problem resolution and predictive maintenance but also hindered the ability to efficiently manage the wide array of pumps installed across various locations.
Unified data platform transforms heat pump management and service
To overcome the challenges of prolonged data analysis and lack of comprehensive insights, Acond embarked on creating a unified data platform leveraging Databricks. They cooperated with the partner DataSentics, a data AI center of excellence within Eviden. The new platform was meant to use data from several thousand modern heat pumps, collating dozens of IoT sensors and hundreds of detailed parameters for each pump, including both historical data and real-time updates.
Real-time adjustments became a cornerstone of the new system, addressing individual pump issues promptly, reducing unnecessary delays and enhancing overall efficiency. The ability for technicians to manage and adjust parameters across all pumps, or selected groups, has drastically changed the maintenance landscape.
Notably, the integration of machine learning has been pivotal. The system now allows for the detection of anomalies in pump behavior, enabling remote predictive maintenance and preventing problems before they escalate. Historical data have been utilized to identify the space containing common device states described by sensorial value combinations. This AI-driven approach not only benefits Acond’s operational efficiency but also enhances customer satisfaction by ensuring reliable pump performance.
The scalability of the Databricks Platform, employing Microsoft Azure, means that as Acond grows and the number of devices expands, the system will adapt and continue to provide valuable, real-time insights and management capabilities.
“The new Aconds’ IoT data platform integrates over 1 billion historical data entries, connects with more than 5,000 devices and processes up to 60 distinct measurements at 5s cycles, generating over 30 million new rows daily. By leveraging Databricks, we have streamlined real-time analytics and predictive maintenance, improving efficiency and scalability while minimizing data aggregation efforts for technicians.”
—Jan Kelbl, Technical Expert, DataSentics
Enhanced efficiency and personalization drive customer satisfaction
The implementation of the unified data platform using Databricks has brought about substantial benefits for Acond and their customers. First, the ability to manage multiple pumps in real time has significantly reduced delays and enhanced overall efficiency. Technicians can now make quick adjustments to individual pumps or groups, effectively personalizing the service based on real-time data.
Moreover, the integration of machine learning for anomaly detection has been bolstered by the resulting equation used to find devices running in an anomalous mode, causing too high energy consumption and increasing the devices’ wear. This enhanced anomaly detection serves as the base for the predictive maintenance solution built on top, meaning issues can be prevented before they escalate, ensuring a higher level of reliability and longer lifespan for the pumps. This proactive approach reduces the need for onsite visits, saving both time and resources for Acond and their customers.
One of the most significant customer-centric benefits is the ability for device personalization. Previously done on request, now each pump can be automatically tailored to the specific needs of each customer based on AI-driven mass personalization. This ensures optimal performance and customer satisfaction.
Lastly, the platform is highly scalable and will grow alongside Acond’s business. It has also provided invaluable insights for the R&D department, aiding in continuous improvement and innovation.